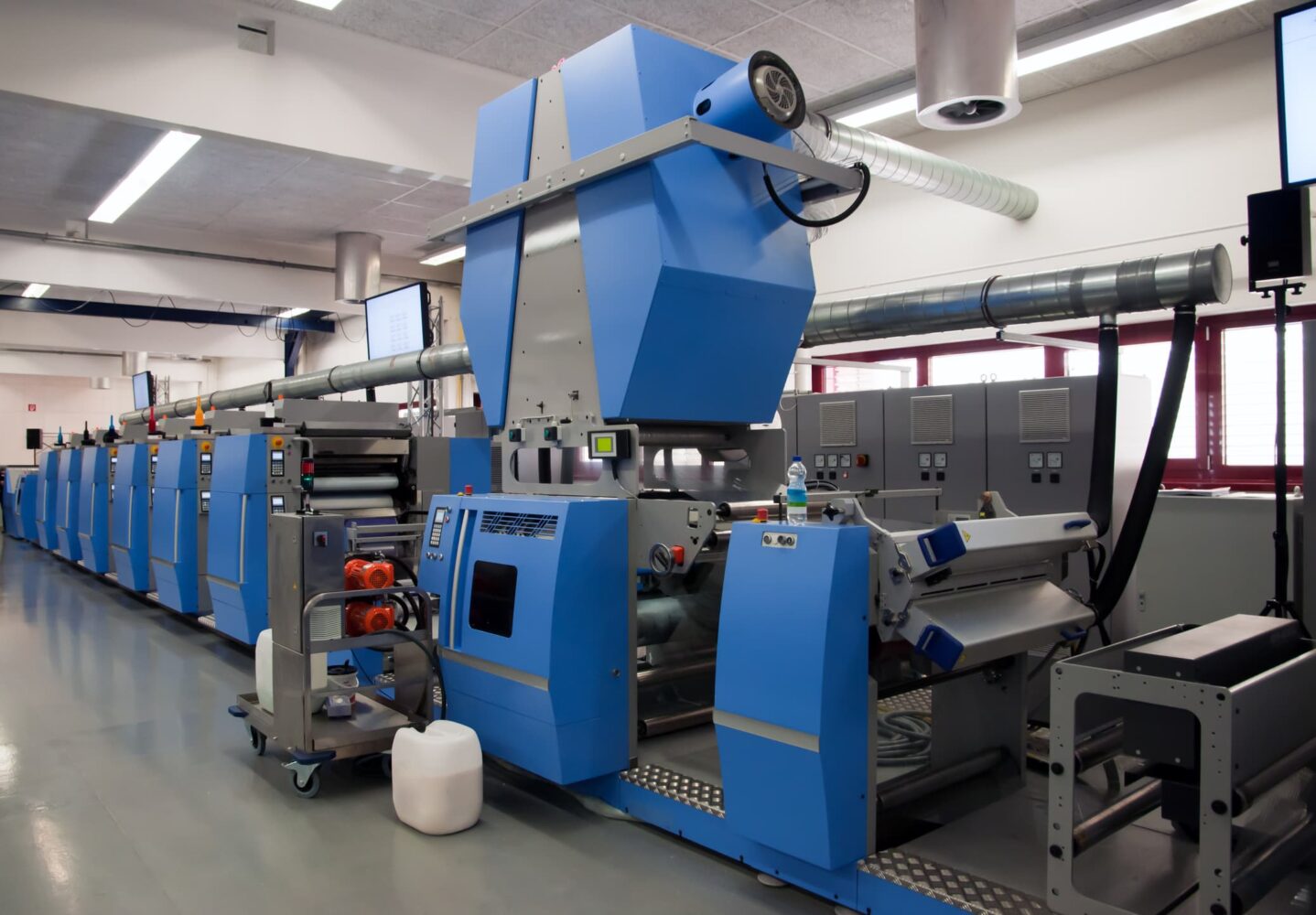
Case Study
Label Plus QLD
Client Background & Project Goals
Persistent & Costly Electrical Failures
Label Plus lead the forefront in print and packaging products for FMCG, pharmaceutical, medical and cosmetic clients. They faced a significant concern, contending with recurrent malfunctions of an electrical circuit board in their digital print press. In previous attempts to manage this persistent issue, they had already implemented 2 replacements, each incurring a cost of $100,000. This seemed to be a temporary fix, which was not financially sustainable.
In search of a lasting solution, Label Plus QLD enlisted Elecstar’s specialised services.
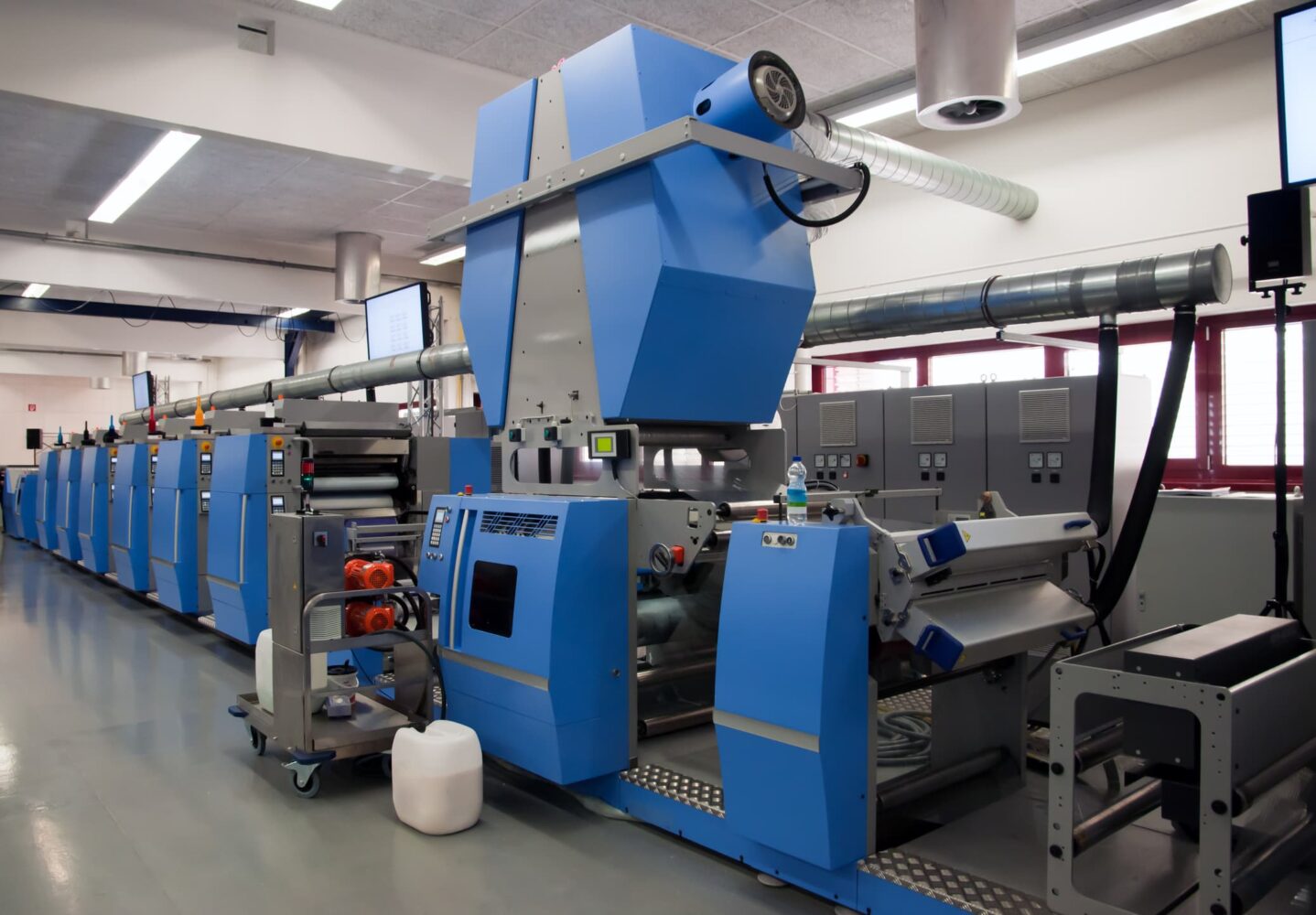
Our Approach & Solution
Optimising Electrical Systems for Efficient Energy Use
Elecstar initiated an exhaustive 7-day evaluation, conducting an in-depth power quality analysis. We provided an engineering report that articulated the power quality issues at hand, followed by specific, actionable strategies for enhancement.
Elecstar proposed and implemented several solutions to address the issue:
Harmonics Filter Installation: Elecstar supplied and installed a harmonics filter to mitigate high harmonics. High harmonics can lead to increased heat in electronic components and reduce their lifespan. By reducing harmonics, the filter helped in preserving the integrity of the electronic components in the print press.
Capacitor Bank Repairs with Power Factor Correction (PFC) Unit: Elecstar installed a Power Factor Correction (PFC) unit. The PFC unit helps in optimising the power factor, which is important for efficient power usage. Improving the power factor ensures that the power supplied is used more effectively and reduces energy waste.
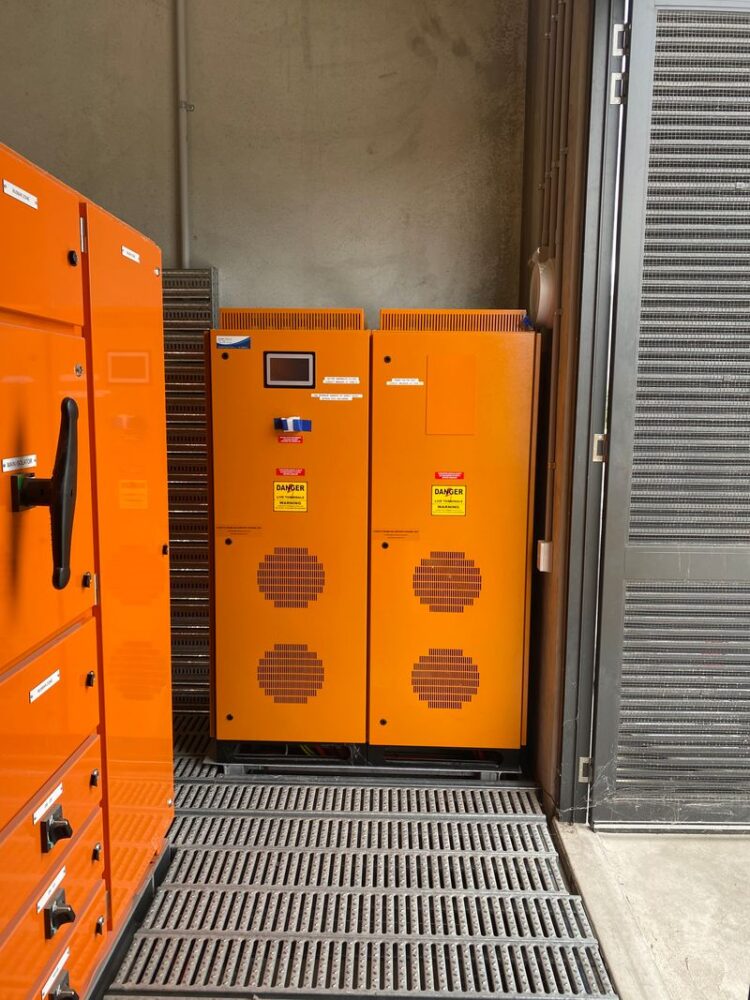
Project Outcome & Final Results
Innovation That Saved Millions
Elecstar’s strategic interventions marked a pivotal moment in addressing the challenges faced by Label Plus QLD, illustrating the indispensable role of expert analysis and targeted solutions in navigating and rectifying complex technical issues effectively.
4 years after implementing these solutions, Labelplus QLD reported significant improvements:
No Further Circuit Board Replacements: With the harmonics filter and power factor correction measures in place, there were no further instances of circuit board malfunction or replacements. This resulted in substantial cost savings, as circuit boards valued at 100,000 dollars each were no longer needed.
Reduced Power Usage: The power quality improvements resulted in reduced power usage, leading to lower energy bills for Label Plus QLD. This is a significant cost-saving measure for any industrial operation.
Elecstar’s solution of installing a harmonics filter and addressing power factor correction not only resolved the immediate issue of circuit board malfunction but also provided long-term benefits in terms of cost savings and improved power efficiency for Label Plus QLD. This case study demonstrates the importance of addressing power quality issues in industrial settings for improved equipment reliability and substantial operational cost savings.